Our global need for greater food security from a sustainable food system could be met with help from big data, artificial intelligence and advanced technology making their way onto the farmer’s field.
AI and new technologies are driving innovation in the agribusiness sector at more than a rapid pace. Companies large and small are thriving in what’s variously called “vertical farming” (due to the inherent physical shape of many new indoor techno-farms) or “controlled environment agriculture” (CEA makes use of various advanced technologies to control light, humidity, soil fertility and other growing conditions).
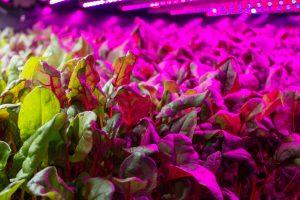
Red chard grows under LED lights at a GoodLeaf indoor vertical farms, where AI-enabled systems and other innovative agritechologies are deployed to grow microgreens and baby greens in Canada year-round. GoodLeaf’s flagship farm is in Guelph, and the company has vertical farm facilities in Calgary, Montreal, and Truro, NS.
Indoor farming operations have rows and rows of plant trays stacked vertically or at an incline, exposed to banks of computer-controlled artificial lighting, often specific-spectrum LEDs. Sensing devices like digital cameras, thermometers, hygrometers and other digital devices capture important crop information and growth data in real-time, which can then be analyzed for efficiency and opportunity.
Advanced technology and AI can stretch the short growing season and reduce the need for fresh produce to be brought in from warmer-climate countries during the winter.
So Canadian governments, funding agencies, and academic researchers are introducing new policies, technologies, and financing to support vertical farming in various ways, and there’ve been successful takers across the countryside and in the big city.
For example, a hands-free vertical farm opened in British Columbia earlier this year, where touchless technology handles everything from seeding to harvest. Of course, successful vertical farms operate in rural and remote areas across Canada, but they’re also growing in urban settings, such as large commercial rooftop greenhouse operations. City buildings are being repurposed, such as the former cereal plant that’s now home to a hydroponic-based agritech facility in Ontario and the Calgary office building where several floors have been rented to an elevated urban farming start-up.
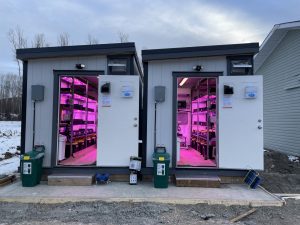
Newly-installed QFarms stand on cement pads beside a building north of Ft. St. James, B.C.; they’ve been installed to help address First Nations and regional food security issues.
At a smaller and more portable scale, Vancouver-based vertical farming company QuantoTech Solutions has successfully deployed what could be dubbed “farms in a box”; the company designs, manufactures, and operates vertical farms to promote food security and sustainability in unconventional climates and under-served communities.
Actually known as QFarms, these versatile vertical farm units can be scaled to fit any location. They feature remote control capabilities over key components such as proprietary high-intensity LED lighting with multiple spectrums, and an integrated hydroponic system that makes use of waste heat from the lights to operate.
And at what’s called the “Brilliant Farm Project”, researchers at Ontario Tech University are developing an energy-efficient CEA facility at Willowtree Farm in Port Perry, Ontario that can outperform traditional greenhouses.
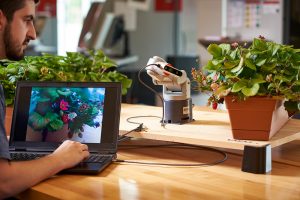
Smaller crops (like strawberries and microgreens) and leafy greens (herbs and lettuces mostly) are leading today’s harvest, and other fruits and vegetables will soon be grown vertically.
Sown by Brilliant Catalyst, the university’s on-campus incubator for innovation and entrepreneurship where startups and researchers develop real-life solutions for growers, the agritech plan recently earned a $1 million development grant from the Weston Family Foundation through its Homegrown Innovation Challenge.
The CEA facility at Willowtree Farm is a thermally-enhanced greenhouse with 350 square metres of dedicated grow space, optimized by artificial intelligence and an Autonomous Intelligent Monitoring System (AIMS) that gathers data about plant health and growth, and can trigger early interventions if plants start to wane.
“The next generation doesn’t see new technology as a threat, they see it as a way to further their legacies,” says Alex McKay, co-owner at Willowtree Farm and a second-generation farmer.
There’s also a combined cooling, heating, and power system at Willowtree that uses organic waste to generate heat and electricity and recycles carbon dioxide back to the plants as nutritional support. Another system runs on captured waste heat from the artificial lights to help control humidity.
Key technology partners on the Ontario Tech Willowtree Project include Canadian agritech companies such as Turnkey Aquaponics and Moduleaf Technologies.
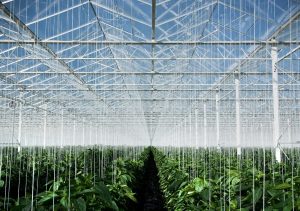
Moduleaf’s Autonomous Intelligent Monitoring System to provides real-time intelligent monitoring of plant health and growth cycles using different sensors and image capture devices.
Based in Oshawa, Moduleaf developed the robotic Autonomous Intelligent Monitoring System that provides real-time monitoring of plant health and growth cycles using different sensors and image capture devices. Collected readings are crunched in various machine learning models to best control the farm environment and get the maximum crop yield.
Turnley Aquaponics is a student-led tech startup that designs, manufactures, and sells equipment and unified systems for the efficient management of power, heat, lighting and data generated in controlled agriculture environments.
“Ultimately an idea such as [the Willowtree energy-efficient CEA facility] this could help mitigate the current food crisis,” says Dr. Osman Hamid, Ontario Tech’s Founding Director of Creativity and Entrepreneurship, and the project’s Principal Investigator. “I think the process is going to be more than fast—it’s going to be hypersonic.”
-30-