A multi-party partnership is putting 3DCP (3D Construction Printing) technology to the test in a proof-of-concept project designed to lead to quicker and more cost-effective housing construction.
The partners are nearing completion on a first-of-its kind home construction project in Leamington, ON, and new 3D printed homes will be move-in ready next month.
Habitat for Humanity Windsor-Essex, the University of Windsor and the Ontario-based technology company nidus3D are working together on the project to design, build and assess the first 3D printed homes for residential use in Canada.
The project will result in a four-plex design, so it’s actually the first such multi-unit residential building in North America. It will be more than 50 by 50 and 30 feet high, the builders describe, resulting in four self-contained housing units each measuring some 560 square feet.
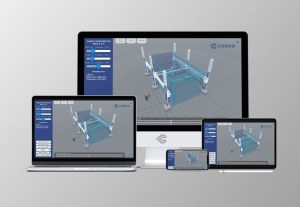
COBOD 3D printing software
And like many more consumer-y 3D printers projects we might be familiar with at home or school, this home-building one is driven by a material-extruding machine controlled by a computer following software instructions to build a larger-than-normal three-dimensional object.
(I still have my first plastic key fob, made using a 3-D printer at the library. But this time, the material is extruded concrete, and the object is someone’s home.)
The company providing the cutting-edge 3D construction technology, nidus3D, is based in Kingston, ON. The firm is a strategic partner and distributor of BOD2 3D printers from a European developer, COBOD.
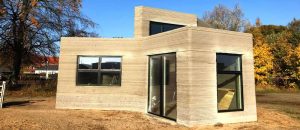
nidus3D printed home in Canada
“In Windsor-Essex alone, there are currently 6,500 individuals that are homeless or at risk of homelessness, and the current solutions are simply not adequate in addressing this issue,” said Ian Arthur, President & Founder of nidus3D, in a release announcing the project. “nidus3D is driven by the mission for increasing access to housing, and we’re deeply honoured for building the first multi-unit 3D printed homes in North America.”
(Arthur knows the area well, and not just because the company he founded is based there. In what is dubbed his ‘post-political career’, Arthur, who was first elected to the Legislative Assembly of Ontario in the 2018 provincial election representing the riding of Kingston and the Islands as a member of the New Democratic Party, is now immersed in the housing construction market as the head of nidus3D.)
Using a modular design that is applicable in many construction settings, the COBOD BOD2 3D construction printer has already been used on multiple projects in Europe and the U.S., printing even larger structures two or three storeys high (10 metres, or 32 feet high) using concrete, mortar or other materials.
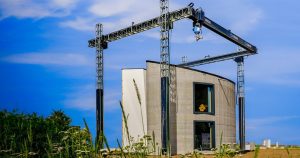
A COBOD 3D construction printer was used Belgian sustainable building company Kamp C to print an entire two-floor, 90 square metre house in Belgium. Kamp C/COBOD image.
Three-dimensional printed buildings can have inner and outer shells for insulation that reduces energy consumption; they can have electrical, IT and other wiring conduits as part of the extrusion blueprint, and additional structures can be added afterwards.
Early 3D printing projects used a lot of cement, the company acknowledges, making its materials recipe too expensive and not CO2 friendly. Now, dry mix 3D printable mortars are being developed as part of a solution for making real concrete from local available materials that can reduce resource and transportation costs. COBOD has investment-type partnerships with other leading international 3D technology development firms, including GE and Peri.
Soon to be ready for occupancy, the nation’s first permitted 3D printed residential homes are being built on the site of The Bridge Youth Resource Centre in Leamington.
“This will be a historic build, the first 3D printed homes for residential use in this country, and potentially a game-changing solution to the current housing crisis,” said Fiona Coughlin, Executive Director & CEO Habitat for Humanity Windsor.
A non-profit organization focussed on affordable housing for all, Habitat Windsor-Essex is working with the University of Windsor to learn more about how this new technology can potentially shorten construction times, and, over time, reduce input costs. “Habitat W-E will benefit from the learning here, and those learnings could have a far-reaching impact for Habitat, and for the construction industry more broadly,” Coughlin added.
“We are very proud to be an active partner and research collaborator in this landmark research project of 3D printed home construction,” said Dr. Sreekanta Das, Professor of Civil Engineering at the University of Windsor.
His team at the Department of Civil and Environmental Engineering in the Faculty of Engineering has been researching the development of environmentally friendly, sustainable printing materials, as well as the applications of 3D printing in construction to resolve the ongoing domestic housing crisis. The project will help form the design codes and standards of future 3D printed constructions and hopefully point the way to lower building costs, increased access and greater availability of resilient, efficient and sustainable housing that’s fully compliant with Canadian building standards.
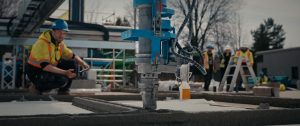
nidus3D crew member operating the 3D printer at the site of The Bridge Youth Resource Centre in Leamington, Ontario. (Photo: Business Wire)
-30-